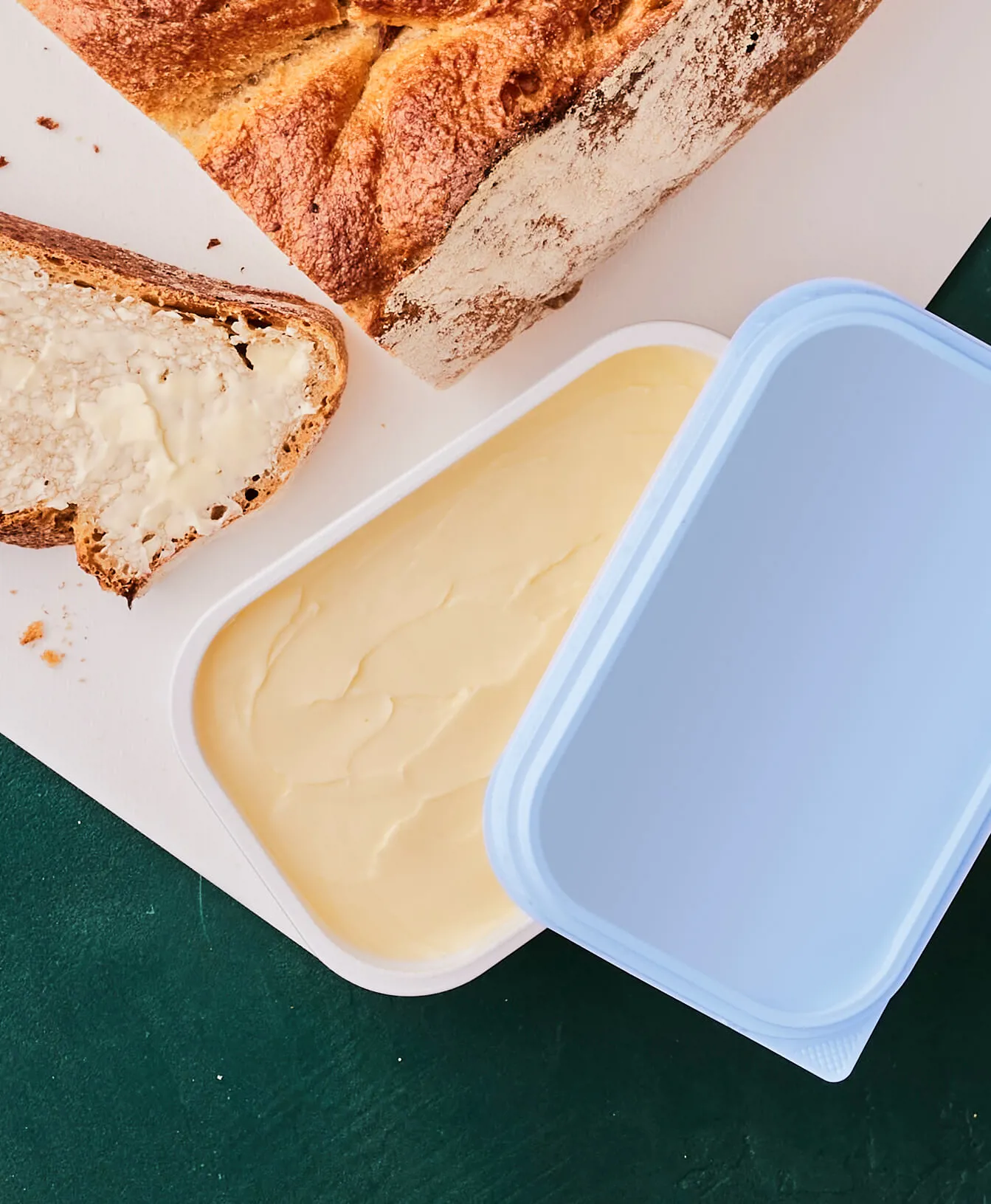
WHITEPAPER
FEATURE ARTICLE
Former Product and Application Manager, Christina Normann Christensen explains the mission and capabilities of the plastics industry’s leading test and processing lab for plant-based polymer additives.
Backed by more than a century of serving the food industry with specialised ingredients, Palsgaard has expanded this extensive knowledge to high-quality food-grade polymer additives serving a wide range of application markets. As plant-based additives, our Einar® products have a perfect fit in packaging and remove consumer concerns about food-contact issues without compromising additive performance.
Today, we develop and validate polymer additives in our state-of-the-art Polymer Application Centre in Denmark, which is fully equipped with advanced facilities for lab-scale testing as well as simulation of real polymer and masterbatch processing environments. Our specialised polymer development team at the Centre uses these capabilities to help us and our customers speed the time-to-market of additive and polymer formulations.
When developing new polymer additives or assisting customers in the evaluation of their polymer solutions, meticulous testing is absolutely vital to succeed. The flexible setup of our Polymer Application Centre provides the capacity and equipment needed to ensure highly precise results with attention to detail across a diverse range of performance criteria. The mission behind all our testing is to provide industry-leading and sustainable polymer additive technology that makes the transition to our plant-based Einar® products as flawless as possible.
Two important properties delivered by Einar® products are anti-static and anti-fog characteristics, as required for maintaining the consumer appeal of transparent plastic packaging. In food applications, these additives prevent moisture formation in the package and dust attraction on the outside. Furthermore, good anti-static performance also facilitates film rolling and eliminates handling problems of moulded end-products on conveyors or stackers. The challenge is to achieve the desired surface modifications to give anti-static or anti-fogging performance without adversely affecting melt and mechanical properties as well as sealabillity. In addition, our specialists at the Polymer Application Centre evaluate the static decay time and surface resistivity of application samples at both ambient and low humidity. Resistance to hot and cold fogging is tested in a 60°C water bath and a 5°C cooling cabinet, respectively.
Most of the testing is targeted at optimising the effectiveness and efficiency of our plant-based additives in polyolefin (PP, PE) film, injection moulding and foam resins. Other tests involve specialised Einar® additives designed to address the mould release of injection moulded products. On a more general level, we also investigate the impact of our additive solutions on the mechanical properties and surface aspects of applications. For customers with specific, intricate anti-static or anti-fogging needs the help of the skilled scientists in Palsgaard’s surfactant R&D centre Nexus is enlisted to create a more tailored Einar® solution for subsequent testing at the Centre.
Typical processing machinery complements the materials test equipment at the Centre. On our injection moulding system, we evaluate the performance of Einar® mould release and anti-static additives mainly in PP, PE and engineering polymers, such as PC.
Dedicated blow moulding equipment allows us to compare the behaviour of Einar® modified polymer applications, particularly PE film, with existing customer solutions using competitive additives. And we are also equipped with a calendaring system for testing e.g. the anti-static and slip properties of primarily PE, PP and PET cast film containing our plant-based additives.
Moreover, by using a specialised combination of filter pressure, particle count and colour strength measurements of samples after processing, we can assess the effective pigment dispersion provided by PE, PP, PVC, PET and PA colour masterbatch formulations with our innovative Einar® dispersing aid.
Altogether, the Polymer Application Centre is an excellent resource for customers who seek to lower their carbon footprint and find out if our sustainable Einar® additives can also improve the quality and performance of their applications. At the same time, the Centre ensures that Palsgaard stays in the lead with plant-based additive solutions for processors, manufacturers and brand owners who wish to take action against the depletion of fossil raw materials and respond to increased consumer demands for more natural product ingredients.
WHITEPAPER
FEATURE ARTICLE
FEATURE ARTICLE
FEATURE ARTICLE
VIDEO FEATURE
FEATURE ARTICLE
TECHNICAL ARTICLE
VIDEO FEATURE
TECHNICAL ARTICLE